It is important to protect workplaces from unwanted accidents and incidents. To help guide you through the wealth of information available, we’ve created this handy guide.
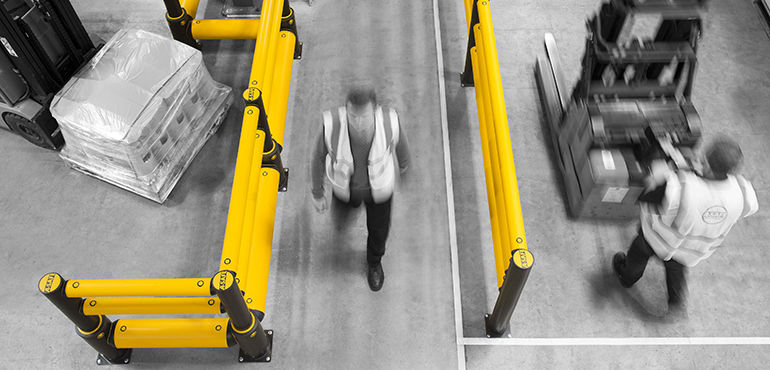
You can read the full article or jump ahead to a relevant section:
- Workplace safety: Understanding the basics
- Workplace hazards: Who and what are at risk?
- Types of workplace risks: What are the hazards?
- Keeping your workplace safe: Who is responsible?
- Workplace safety: Standards and regulations
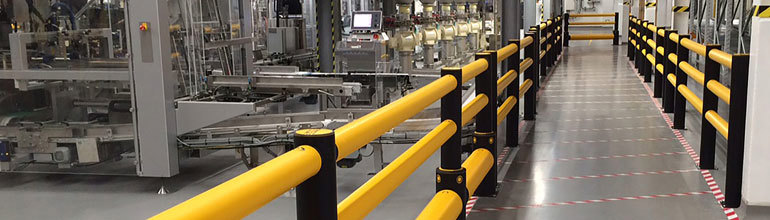
1. Understanding the basics
Keeping a workplace safe comes from a combination of common sense and planning. By learning about and identifying potential risks, you can prevent or control them. Once the proper measures are in place, it’s just a matter of using common sense to ensure they are being followed by everyone on site.
What is workplace safety?
Workplace safety refers to the rules, regulations and guidelines that keep corporate and industrial working environments safe during day-to-day operations. Some of these rules will be outlined in official regulations, some with be unique to individual industries or workspaces, and some will be common sense approaches that keep people safe while at work.
What are the risks of not keeping a workplace safe?
It is important to keep workplaces safe to avoid any unwanted accidents or incidents. These incidents can range from minor inconveniences that slightly hinder people from completing their duties to complete stoppages in work. These serious issues could include accidents that cause severe injury to workers or even death and substantial damage to valuable assets or infrastructure.
Risks vary depending on several factors:
- The type of workplace
- The type of work undertaken in that facility or office
- Environmental factors – such as outdoor work, working at specific temperatures, etc.
- Additional factors such as site vehicles, complex machinery and specific equipment
In addition to the harm or damage that could befall people and assets, other consequences of not providing the proper workplace protection include the slowing down or stopping of production, downtime for repairs and maintenance, and the threat of prosecution or fines as a result of not following the correct safety measures.
Now you understand the basics of safety in the workplace, find out how we can help you assess risks at your facility and find the most effective solutions to your safety needs. A member of the A-SAFE team will be more than happy to help with on-site or remote support.

2. Workplace hazards | Who and what are at risk?
The three areas of concern are:
- People (staff, contractors, visitors, etc.)
- Infrastructure (the building, structural weak points, etc.)
- Assets (stock, machinery, equipment)
People
It goes without saying that people need protecting. Whether they are your workers, visitors to site, contractors or any other number of people who could be at your facility at any given moment, measures need to be in place to ensure they can work and travel through your facility safely.
Infrastructure
At busy sites and facilities, damage to infrastructure, including walls, doorframes and flooring, is incredibly common. However, it’s important to have procedures in place to ensure these are properly protected too. That may mean minimizing scuffs and knocks to corners or providing more robust protection for support beams or columns. It could even be maintaining the areas of your site that are prone to wear and tear, such as carpets or tiling.
Assets
The term ‘assets’ can seem quite ambiguous but actually it covers most valuable things at your facility that are worth protecting. Machinery, vehicles and equipment are all vital to the smooth running of your business, so they must be protected to prevent not only injury but also outages and downtime.
Stock is also classified as ‘assets’. Your stock is incredibly valuable, so it’s important to ensure that the stock itself, as well as the storage facilities you use, are properly protected.
Once you identify who and what is at risk at your facility, you can start to zero in on the right protection for each area. At A-SAFE, we understand workplace safety needs and can help you find the right solutions.
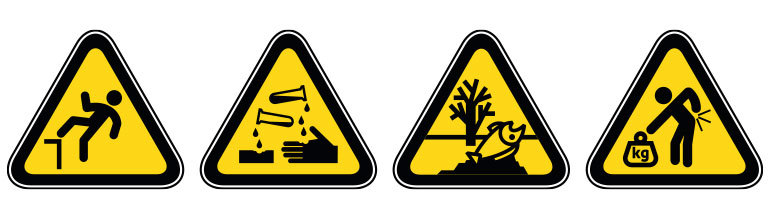
3. Types of workplace risks| What are the hazards
There are a range of risks to look out for in the workplace. As mentioned above, these depend on the types of industry and workplace.
The U.S. Occupational Safety and Health Administration identified four primary types of hazard that occur in most workplaces:
Physical hazards
These hazards are the most common and can make the workplace an unsafe environment. They include hazards such as dangerous drops, spills, trips, exposed wires as well as more environmental factors such as excessive noise, high or low temperatures and sources of radiation.
Chemical hazards
This refers to chemicals in the workplace that are dangerous or highly volatile. These could present a specific danger to people and assets. In many cases these chemicals could lead to irritation, burning or fatalities.
Biological hazards
Mainly referring to specific working conditions, biological hazards include workers being exposed to harmful bacteria, viruses, molds and microorganisms likely to cause infection. This includes untreated sewage, hypodermic needles and rotting food.
Ergonomic hazards
When we talk about ergonomic hazards, this refers to the way people work and the tasks or motions that could adversely affect them. That could include heavy lifting, repetitive motions and working conditions that impact on people’s posture and comfort.
How do you spot potential hazards in the workplace
The best way to identify potential workplace hazards is by performing a thorough risk assessment. Reviewing your facility and observing how people work and interact with equipment and each other allows you to identify where there is the potential for accidents, where people or assets are at risk of harm, or areas where proper safety measures are not in place.
If you need help identifying the relevant risks to your site, then we can help. At A-SAFE, our team can perform a site survey, either remotely or in person, and help you find the right protection.
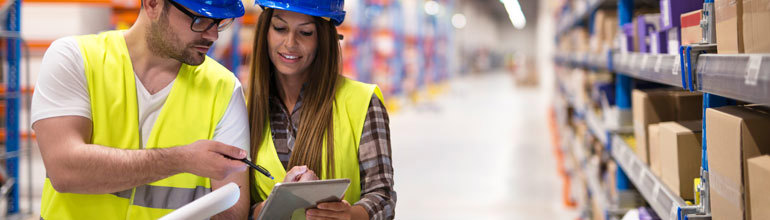
4. Keeping your workplace safe | Who is responsible?
Spotting the risks and hazards at a site is one thing, but how do you ensure these issues have been raised and whose job is it to ensure they are resolved?
How do you keep workplaces safe?
There are lots of ways to ensure your workplace is safe. These include:
- Accident reporting
- First aid materials and training
- Effective training for machinery and equipment operators
- Fire and emergency procedures
- Use of personal protective equipment (PPE)
Some of these are mandatory, others depend on the type of work environment and the duties required of people on site. Regardless, it is always important to be aware of applicable safety measures – even if they don’t directly relate your job (for example, fire and emergency procedures).
Who is responsible for keeping a workplace safe?
It is an employer’s responsibility to ensure that everyone and everything in their business is properly protected. It is up to them to identify potential risks and problems and put measures in place to prevent or minimize these occurrences. It is a legal requirement for employers, but it is also in their best interest. Minimizing risk will reduce the chance of damage occurring to valuable stock or infrastructure and avoid prolonged periods of downtime caused by on-site accidents.
Who implements safety on site?
In terms of leading the safety of a workplace, an employer might delegate responsibility to a designated member of the senior management team. This person could have one of several different titles; however, the most common is “Health and Safety Manager”. This is someone who’s sole duty is to ensure a workplace follows government guidelines and best practice regulations. They make sure that a facility and the people within it are compliant with the governmental regulations.
Other roles that may take on responsibility for workplace safety can include:
- Operations managers and directors
- Warehouse or factory managers
- Office managers
- Maintenance teams
- Members of the human resources department
Ultimately, everyone is responsible for following the safety procedures and guidelines at a place of work. By adhering to the rules of the workplace, everyone can minimize the potential for accidents.
At A-SAFE, we understand the problems and issues Health and Safety Managers face, from finding affordable solutions to getting safety systems signed off by upper management. We can provide you with all the relevant information and date you need to prove how essential site safety is at your facility. Get in touch to see how we can help.
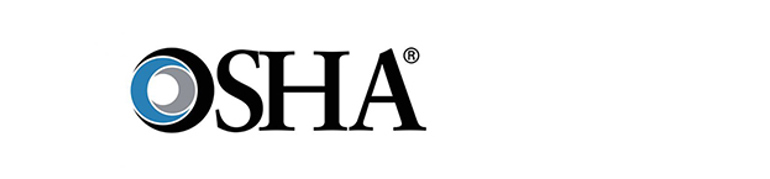
5. Safety standards and regulations
With issues as important as safety, there are clear rules and regulations around what is expected from employers and employees. This section looks at who controls and implements the relevant safety standards.
Who oversees workplace safety regulations?
The Occupational Safety and Health Administration (OSHA) is the U.S. agency responsible for the regulation and enforcement of workplace safety. OSHA was created in 1970 with the signing of the Occupational Health and Safety Act. The agency’s mission is to protect the health, safety and welfare of workers, and as a result, its website is full of useful information and guidance for both employees and employers.
To achieve its mission, OSHA sets workplace safety regulations, including developing health and safety standards, responding to complaints and providing safety training, outreach and education.
What are OSHA’s reporting guidelines for fatalities, hospitalizations and amputations?
OSHA has reporting standards that workplaces are required to adhere to, and parts of Standard 1904 require employers and those in charge of safety and operations at work premises to report serious workplace accidents. For example, employers and/or safety managers must report the death of an employee as the result of a work-related incident within 8 hours. Similarly, an incident that involves an amputation, the loss of an eye or requires in-patient hospitalization must be reported within 24 hours.
What are the rules for safety barriers at a workplace?
OSHA sets forth its standards for guardrails and barriers in Standard 1910.29, which covers fall-protection systems and practices. Further details on this standard are discussed in numerous standard interpretation letters, which provide clarification based on questions from the public about this standard (and many others, too).
What are an employer’s responsibilities regarding hazardous substances in the workplace?
Employers have numerous responsibilities that are tied to workplace safety, according to OSHA, some of which are focused on hazardous substances. Employers with operations that utilize hazardous chemicals in the workplace must develop and implement a written Hazard Communication Standard (HCS) program and train employees on the hazards they are exposed to and proper precautions to minimize risks. Employers must also make readily available a copy of safety data sheets for known hazardous substance.
Aside from its general standards for forklifts (also known as powered industrial trucks), OSHA has established specific standards for when forklifts transport hazardous materials.
Where can I find the general regulations around safety in the workplace?
The rules and guidelines for workplace safety in the United States are outlined in OSHA’s Standard 1910, which offers dozens of standards put in place to protect workers.
OSHA also offers eTools to discuss best safety practices in the workplace. These include forklift operation tips and how forklift operators and pedestrians should be mindful of one another.
Other nations have agencies like OSHA in place to protect the health, safety and welfare of workers. Globally, there is the International Standards Organization which provides global standards for safety systems.
At A-SAFE, our safety solutions are compliant with the relevant safety standards and codes of practice. Our barriers are the most heavily tested in the world, this is to ensure they provide ultimate protection. It’s peace of mind when you need it most. For more information, contact us.
Learn more about what we can do
Safety in the Workplace | A summary
There is a lot to know when it comes to workplace safety, but much of it is common sense. With a little research, you can understand what risks are present on site and how best to tackle them.
We are committed to understanding workplace safety and helping to make industrial facilities safer by creating more advanced solutions. A-SAFE can help you with a range of polymer safety products and more. Contact a member of our team to find out how we can help you. Give us a call on (443) 776-3472, email us at [email protected] or use the contact form below and see how we can help you.